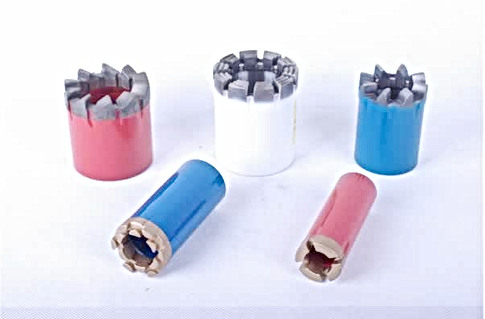
The diamond drill bit for hard rocks is a top-notch drilling tool designed to efficiently and accurately drill through hard rocks and minerals. Its diamond-coated surface ensures a long lifespan and excellent performance, making it a reliable choice for professionals.
The bit's high-quality steel shank provides durability and strength, ensuring stability during the drilling process. The advanced cooling system helps to prevent overheating, ensuring that the bit remains cool and stable even during extended use.
The diamond drill bit is available in various sizes to accommodate different drilling needs, making it versatile and suitable for various applications, including geological surveying, mining, and construction. Its long lifespan and cost-effectiveness make it a valuable tool for any project that requires drilling through hard rocks and minerals.
Professionals can use the diamond drill bit for hard rocks to ensure accurate results and reduce the risk of errors. The bit is easy to use and requires minimal maintenance, making it a convenient choice for those who need a reliable drilling tool.
With its durable construction, advanced design, and versatility, the diamond drill bit for hard rocks is an excellent choice for anyone looking for a reliable and efficient drilling tool. Its long lifespan, cost-effectiveness, and ease of use make it a valuable tool for any project that requires drilling through hard rocks and minerals.
Features:
Higher Diamond Concentration:
Similar to the previous description, higher diamond concentration is emphasized. This results in increased tool life and penetration rates, making the drill bit suitable for challenging rock formations.
Lower Fuel Consumption and Less Equipment Wear:
The design aims to minimize fuel consumption and reduce equipment wear, contributing to cost-effectiveness and prolonged equipment life.
Simplified Matrix Choice for Reduced Inventory Costs:
The matrix, the material that holds the diamonds in the bit , is chosen to be simplified. This simplification helps in reducing inventory costs, providing economic benefits.
Applications:
The diamond drill bits are versatile and find applications in various fields:
Hard Rock Drilling:
The primary purpose is drilling through hard and dense rocks where general diamond bits may face challenges.
Metal Exploration:
Used in metal exploration activities where drilling through challenging geological conditions is required.
Coalfield Mining:
Applicable in drilling for coalfield mining operations in hard rock environments.
Geological Exploration:
Used for obtaining core samples in geological exploration activities, especially in areas with hard rock formations.
Water Well Drilling:
Suitable for drilling wells in regions where the subsurface consists of hard rocks.
Hydropower and Water Conservancy:
Used in projects related to hydropower generation and water conservation where drilling through hard rock formations is necessary.
Construction Industry:
Applicable in various construction projects, including road, bridge, railway, and building construction, where drilling into hard rock is required.
Overall, this diamond drill bit for hard rocks is designed to offer a cost-effective and efficient solution for drilling in challenging geological conditions, providing durability and enhanced performance in specific applications.
How to Buy
Request an Equipment Quote
Ready to buy stuff from Flexible,Request a quote now.
Buy
Browse Parts and equpments on our store
Reviews
FAQ
Q: What are the most common types of drilling method?
Here are the five common types of oil drilling techniques. 1. Cable Drilling. 2. Directional Drilling. 3. Electro-Drilling. 4. Rotary Drilling. 5. Dual-Wall Reverse- 6. Circulation Drilling.
Q: How deep can a drill rig go?
Depending on the rig type, offshore rigs are rated to drill in water depths as shallow as 80 feet to as great as 12,000 feet. The greatest water depth a jackup can drill in is 550 feet, and many newer units have a rated drilling depth of 35,000 feet.
Q: What is the process of oil exploration?
Oil and gas exploration encompasses the processes and methods involved in locating potential sites for oil and gas drilling and extraction. Early oil and gas explorers relied upon surface signs like natural oil seeps, but developments in science and technology have made oil and gas exploration more efficient.
Q: What are the positions on a rig?
Diver – Some rigs require the use of divers to maintain the underwater equipment. Driller – Heads up all operations related to the drilling equipment. Electrician – Maintains and repairs all electrical systems onboard the rig. Floorman – Provides general support to the rig's drilling operations.